In the world of technical ceramics, there are two materials that are surpassed only by diamond and cubic boron nitride in terms of hardness – and both are used by China Ceramic Parts, Inc. as a base material for a wide range of technical components in an equally wide field of applications.
Boron Carbide (B4C) is currently the hardest material produced in tonnage quantities and is the third hardest material known to man after diamond and cubic boron nitride. Not far behind it in the hardness stakes comes silicon carbide (SiC), steeped in history since it was first mass-produced in 1893 and probably the most common of all industrial abrasives.
B4C
The extreme hardness of boron carbide provides excellent wear and abrasion resistance and,
consequently, it is a perfect base material for the manufacture of nozzles for slurry pumping, grit
blasting, and water jet cutters.
In combination with other materials, boron carbide also finds extensive use in ballistic armor (including body and personnel armor), where its combination of high hardness, high elastic modulus, and low density gives the material exceptionally high specific stopping power to defeat high velocity projectiles.
Other applications include ceramic tooling dies, precision tool parts, jigs, and other high wear
applications.
SiC
The technical properties of silicon carbide are remarkably similar to those of diamond. It is one of the lightest, hardest, and strongest technical ceramic materials and has exceptional thermal conductivity, chemical resistance, and low thermal expansion.
Silicon carbide is an excellent material to use when physical wear is an important consideration, because it provides good erosion and abrasive resistance, making it particularly suitable for such applications as spray nozzles, shot blast nozzles, and cyclone components.
Not so long ago, silicon carbide was the chosen material to line the brakes of the most advanced, jaw-dropping cars the world has ever seen; the McLaren P1 for example.
DuraWear, a hybrid combining the benefits of Boron Carbide (B4C) and Silicon Carbide (SiC), this material evolved to retain the incredible hardness of both materials, without some of the constraints of either. This hybrid offers the benefits of a high melting point, good thermal shock resistance, and is chemically inert.
DuraShockTM, a hybrid also combining B4C and SiC, but focused on ballistic applications, this light but incredibly hard material can withstand some of the latest threats, while being much easier to produce than pure Hot Pressed Boron Carbide.
CeramAlloy Ultra Hard, a Zirconia Toughened Alumina (ZTA), an oxide ceramic, this material combines high hardness with good fracture toughness and good bending strength. The material is also “hipped” (Hot Isostatic Pressed), a process which applies extreme pressure and high temperature at the same time, further enhancing the material and giving it excellent consistency.
Our in-house Hipping process is utilized with many of our ultra-hard and ultra-tough materials to take
those materials to another level.
These materials sit tall on the shelves of the China Ceramic Parts raw materials stores. And that’s why they continue to provide the very highest level of performance to China Ceramic Parts, Inc. customers worldwide in a wide field of applications.
It’s tough at the top…
And to be at the top, you have to be tough. These materials sit tall on the shelves of the Precision
Ceramics raw materials stores. That is why they continue to provide the very highest level of
performance to China Ceramic Parts customers worldwide in a wide field of applications.
Further detailed technical and applications information and downloadable data sheets are available for all our materials from the China Ceramic Parts, Inc. website.
The below data table compares the Hardness and Fracture Toughness (with indicative values) of the 4 materials mentioned.
Compound
ID
Hardness
Fracture Toughness
Compound
ID
Hardness
Fracture Toughness
Compound
ID
Hardness
Fracture Toughness
Compound
ID
Hardness
Fracture Toughness
Compound
ID
Hardness
Fracture Toughness
View the full range of ceramic materials offered by China Ceramic Parts, Inc.
Related Materials
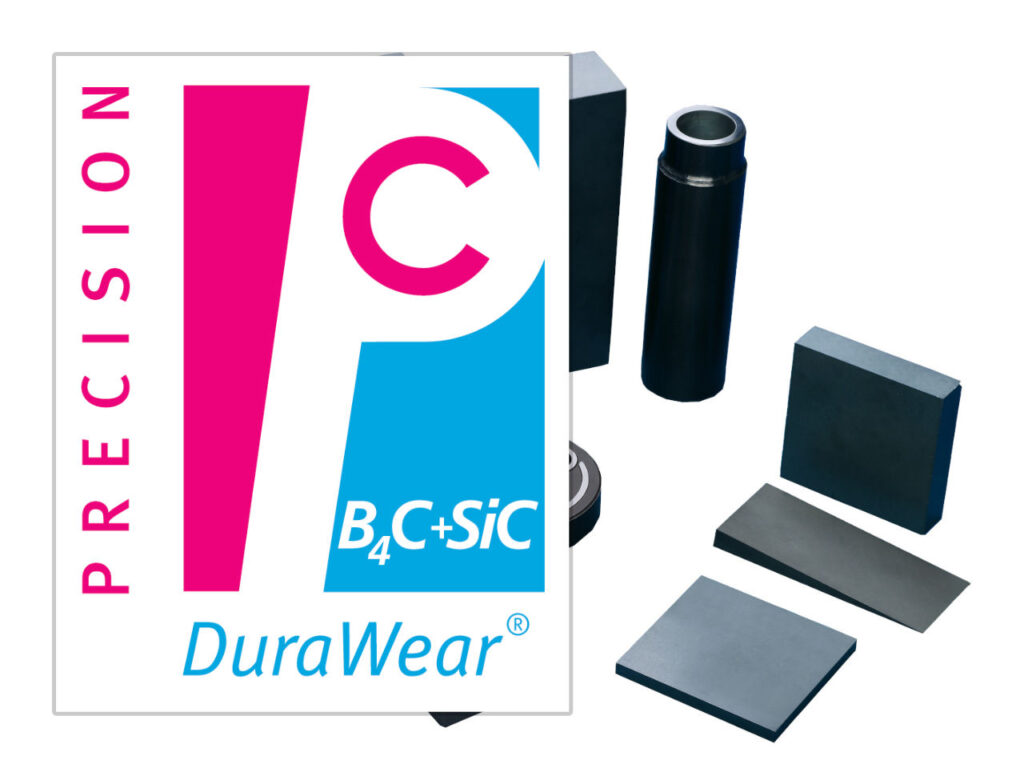
Boron Carbide
DuraShock™ & DuraWear™
Boron Carbide (B4C), also known as black diamond, is the third hardest material after diamond and cubic boron nitride. It is a suitable material for many high performance applications due to its attractive combination of properties.
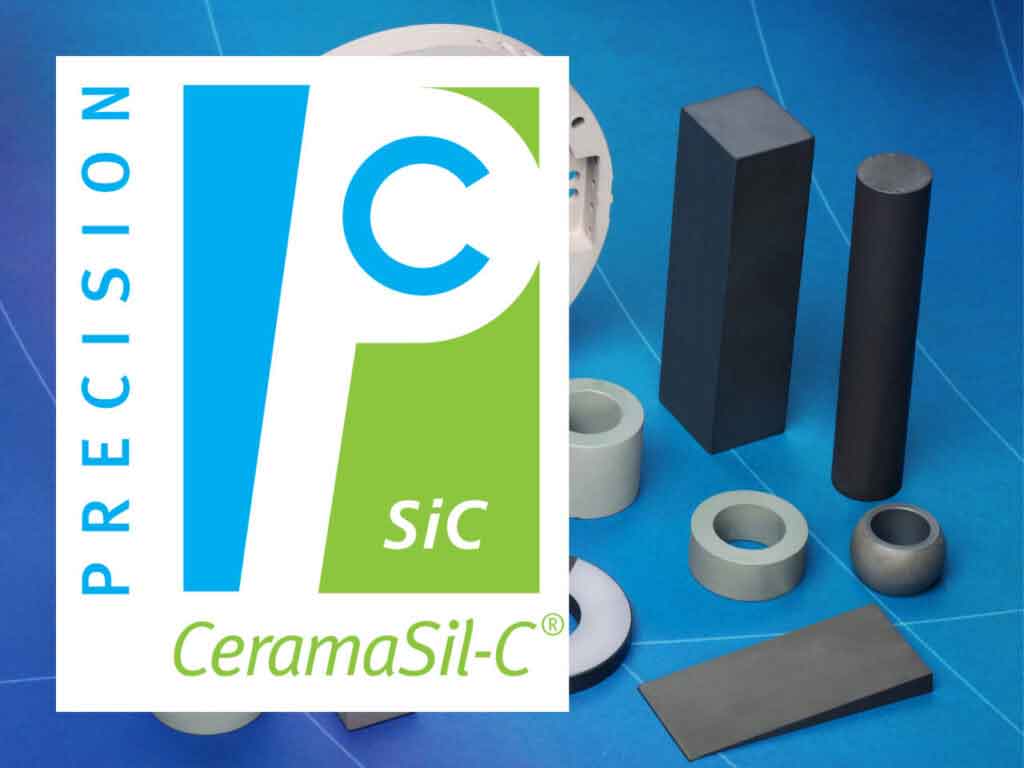
Silicon Carbide
CeramaSil-C™
Silicon Carbide (SiC) is one of the lightest, hardest, and strongest technical ceramic materials with exceptional thermal conductivity, acid resistance, and low thermal expansion.