Ceramics in the Medical Industry
Technical Ceramics are becoming more prevalent in the medical industry because they are non-magnetic, do not conduct electricity, and do not outgas.
In the medical industry, the reliability and accurancy of products are paramount and Technical Ceramics are known for their reliability and consistency in applications. In the medical field, devices and components often endure high voltages and temperatures when in use and Technical Ceramics can withstand these without incurring any damage or reduction in functionality.
Technical Ceramics are chosen for their critical functionality and reliable performance in the field, including the following advantages:
- Flexural strength
- Biocompatibility
- Chemical resistance
- Density and stiffness (Young’s modulus)
- Compressive strength
- Electrical insulation
- Dielectric strength
- Hardness
- Corrosion resistance
- Food compatibility
- Piezoelectricity and dynamics
- Temperature resistance
- Thermal shock and fluctuation resistance
- Metalization (joining technology)
- Wear resistance
- Thermal expansion
- Thermal insulation
- Thermal conductivity
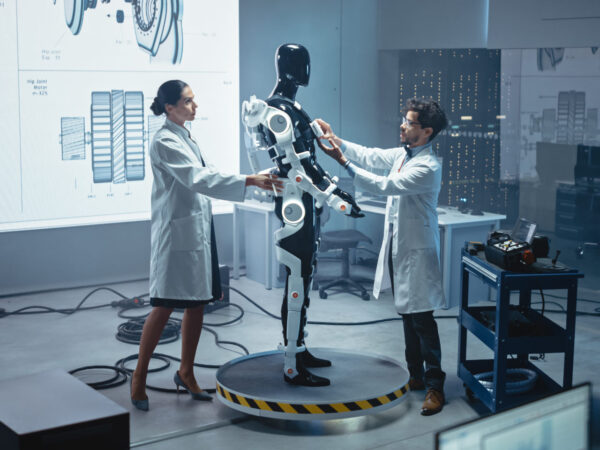
In-Body Devices
Technical Ceramic materials are used for modern medical processes and in-body devices such as bones, joints, teeth, and other medical applications.
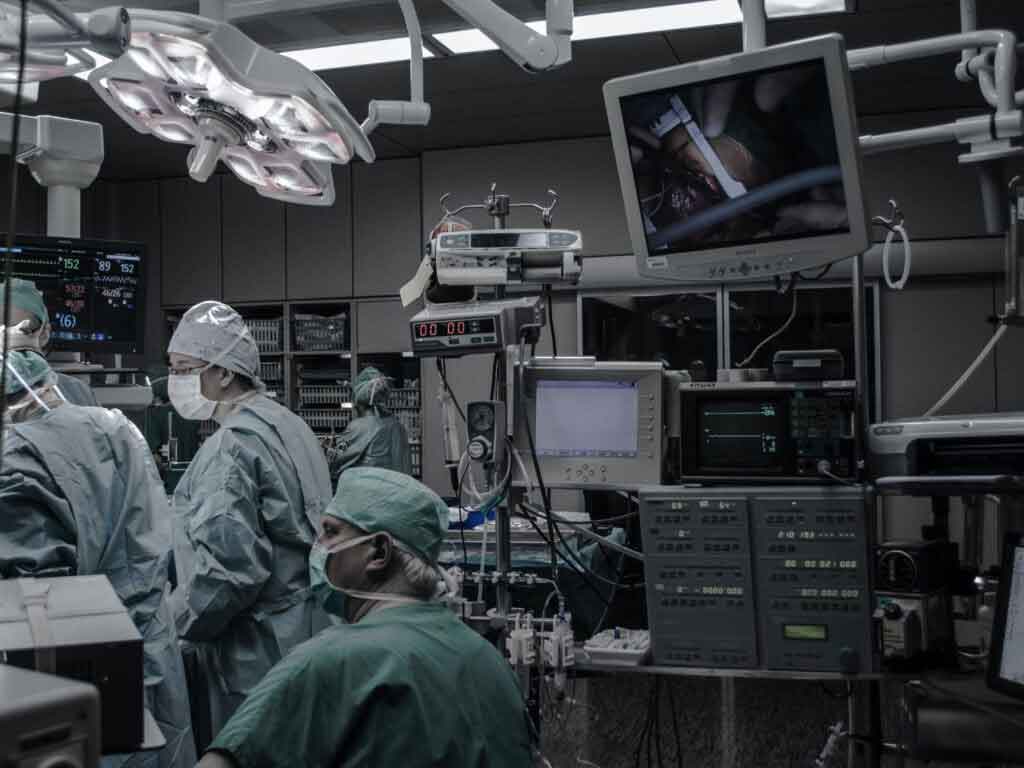
Medical Instruments
Technical Ceramics are an ideal material for medical instruments and products due to their superior dimensional stability, physical wear, and strength.
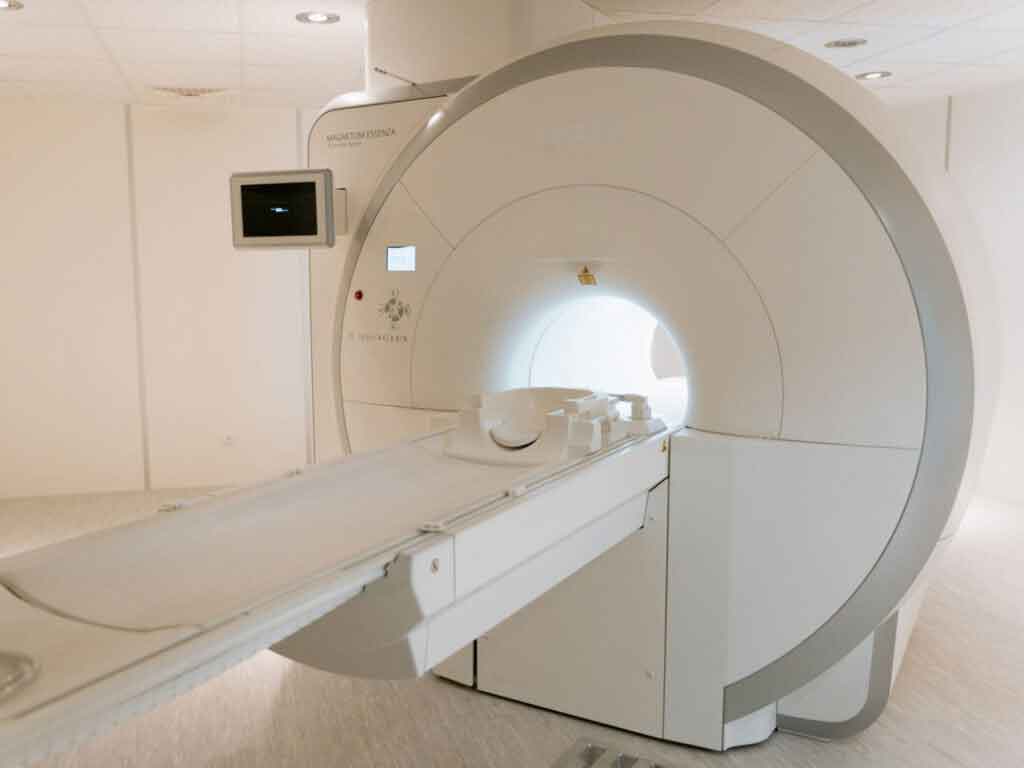
MRI Scanners
MRI scanners use strong magnetic fields and radio waves to form images of the body and ceramics are among the most well-known electrically insulating materials.
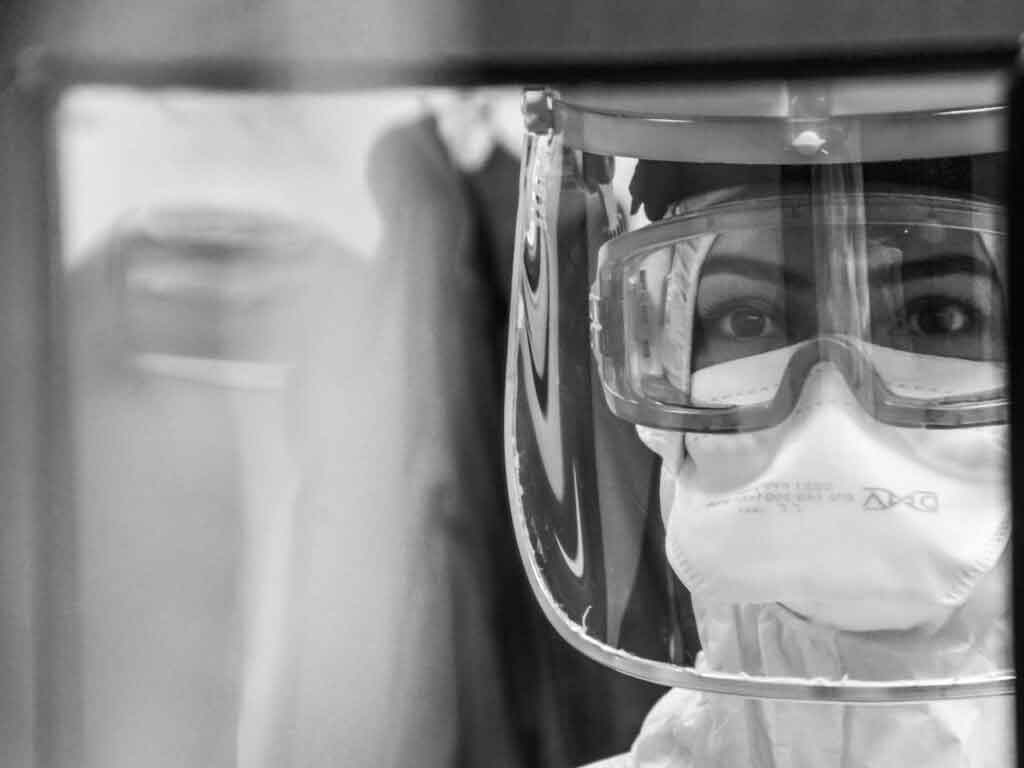
PPE & Health Protection
Printing using Technical Ceramic parts have been instrumental in the labeling of PPE, including the marking and coding of masks, respirators, gloves, bottles for fluids, etc.