Boron Carbide (B4C)
Boron Carbide (B4C), also known as black diamond, is the third hardest material after diamond and cubic boron nitride. It is a suitable material for many high performance applications due to its attractive combination of properties. Its outstanding hardness makes it a suitable abrasive powder for lapping, polishing and water jet cutting of metals and ceramics. The combination of low specific weight, high hardness and reasonable toughness makes it a suitable material for body and vehicle armor. Boron carbide is also extensively used as control rods, shielding materials and as neutron detectors in nuclear reactors due to its ability to absorb neutrons without forming long lived radionuclide. As it is a p-type semiconductor, boron carbide can be a suitable candidate material for electronic devices that can be operated at high temperatures. Boron Carbide is also an excellent p-type thermoelectric material.
Boron Carbide Properties
- High hardness
- Low density
- High melting point
- High elastic modulus
- Chemical inertness
- High neutron absorption cross-section
- Excellent thermoelectric properties
Related Materials
DuraShock and DuraWear are new ranges of boron carbide-based ceramic composites. They are manufactured ‘in-house’ and are ideal for applications where high hardness, impact resistance, and tolerance to abrasive wear is required.
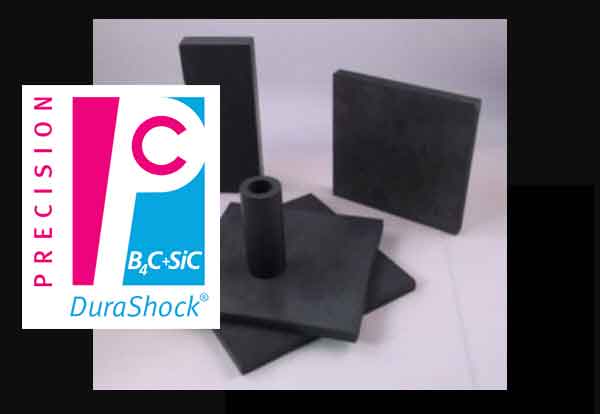
DuraShock (Boron Carbide & Silicon Carbide Composite)
Boron carbide, also known as black diamond, is the third hardest material after diamond and cubic boron nitride. It is a suitable material for many high performance applications.
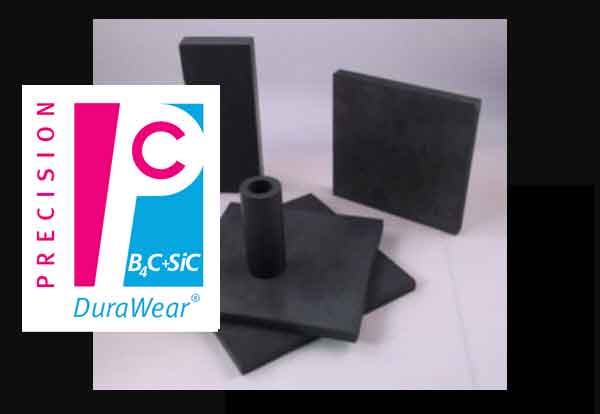
DuraWear (Boron Carbide & Silicon Carbide Composite)
Boron carbide, also known as black diamond, is the third hardest material after diamond and cubic boron nitride. It is a suitable material for many high performance applications.
Boron Carbide Manufacturing
Boron Carbide can be machined in green, biscuit, or fully dense states. While in the green or biscuit form it can be machined relatively easily into complex geometries. However, the sintering process that is required to fully densify the material causes the Boron Carbide body to shrink approximately 20%. This shrinkage means that it is impossible to hold very tight tolerances when machining Boron Carbide pre-sintering. In order to achieve very tight tolerances, fully sintered material must be machined/ground with diamond tools. In this process a very precise diamond coated tool/wheel is used to abrade away the material until the desired form is created. Due to the inherit hardness of the material, this can be a time consuming and costly process.
Frequently Asked Questions
- What is Boron Carbide used for?
The combination of low specific weight, high hardness and reasonable toughness makes it a suitable material for body and vehicle armor. Boron carbide is also extensively used as control rods, shielding materials and as neutron detectors in nuclear reactors due to its ability to absorb neutrons without forming long lived radionuclide. As it is a p-type semiconductor, boron carbide can be a suitable candidate material for electronic devices that can be operated at high temperatures. Boron Carbide is also an excellent p-type thermoelectric material. Some typical applications of boron carbide include:
- Sand blasting nozzles
- Ball & roller bearings
- Seals
- Wire drawing dies
- Body armour