Alumina (Aluminum Oxide)
Alumina, also known as Aluminum Oxide, is a hard wearing advanced technical ceramic material frequently used in a wide variety of industrial applications. Once fired and sintered, it can only be machined using diamond-grinding methods. It features high hardness and wear resistance, low erosion levels, high temperature resistance, corrosion resistance, and bioinertness. Additionally, it can be highly polished making it useful for precision sealing applications like pumps and pistons.
Alumina is an excellent high temperature ceramic material due to its high temperature stability. It is the most commonly used type of advanced ceramic and is available in purities ranging from 95 – 99.9%. China Ceramic Parts has access to many different types of Alumina including: injection molded, die pressed, isosostatically pressed, slip cast, and extruded.
Alumina Properties
Alumina features high hardness and wear resistance, low erosion levels, high temperature and corrosion resistance and bio-inertness. Its high temperature stability and thermal conductivity make it particularly suitable for high temperature applications such as thermocouple protection in high temperature measurement.
- Excellent electrical insulation properties
- High compressive and dielectric strength
- High hardness and mechanical strength
- High thermal conductivity and thermal shock resistance
- Low density
- Resistant to strong acid and alkali attack at high temperatures
- Transparent to microwave radio frequencies
- Very specific thermal conductive and thermal expansion rates
- Wear and abrasion resistant
Alumina is available is multiple grades including 95%-99.9% high purity Alumina, high purity re-crystalized Alumina, and Zirconia toughened Alumina (ZTA). The following are the properties for 99.7% grade alumina.
Mechanical Properties
Density
Compressive Strength
Tensile Strength
Flexural Strength @ 20°C
Flexural Strength @ 800°C
Fracture Toughness KIc
Young‘s Modulus E
Poisson Ratio
Hardness Knoop (1000g)
Unit
Value
Thermal Properties
Maximum Temperature
Thermal Conductivity @ 20°C
Thermal Expansion a at 20–100°C
Specific Heat
Thermal Shock Parameter R1
Unit
Value
Electrical Properties
Dielectric Constant
Dielectric Strength (6.35mm)
Dielectric Loss (tan delta 25° C)
Volume Resistivity @ 25°C
Volume Resistivity @ 500°C
Volume Resistivity @ 1000°C
Unit
Value
Related Materials
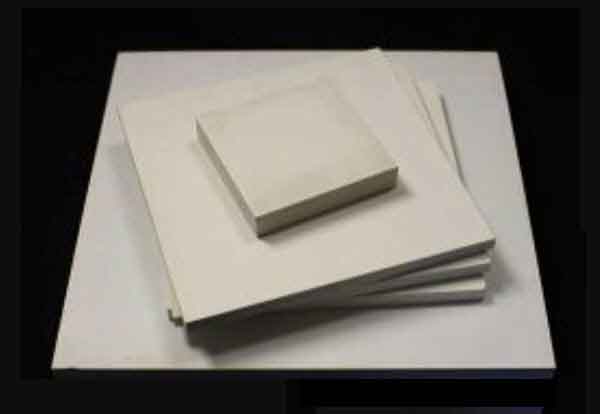
Aluminum Nitride
Aluminum Nitride (AlN) is an excellent material to use if high thermal conductivity and electrical insulation properties are required -- an ideal material for use in thermal management and electrical applications.
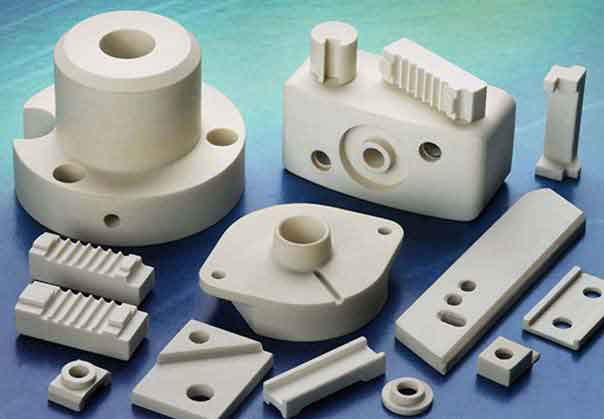
Shapal Hi-M Soft
Shapal Hi-M Soft is a hybrid type of machinable Aluminum Nitride (AlN) ceramic that offers high mechanical strength and thermal conductivity.
Alumina Manufacturing
Alumina can be produced in a wide range of purities with additives designed to enhance its properties. Typical purities range from 90 to 99.9% although China Ceramic Parts generally work with 99.7% material.
It can be injection molded, die pressed, isostatically pressed, slip cast and extruded. Once fired and sintered, it can only be machined using diamondgrinding methods but prior to sintering advanced green and biscuit machining techniques developed by China Ceramic Parts allow more complex components to be manufactured using traditional machining methods. In addition Alumina can be readily joined to metals or other ceramics using metallising and brazing techniques.
Alumina can be machined in green, biscuit, or fully dense states. While in the green or biscuit form it can be machined relatively easily into complex geometries. However, the sintering process that is required to fully densify the material causes the alumiuna body to shrink approximately 20%. This shrinkage means that it is impossible to hold very tight tolerances when machining alumina pre-sintering. In order to achieve very tight tolerances, fully sintered material must be machined/ground with diamond tools. In this process a very precise diamond coated tool/wheel is used to abrade away the material until the desired form is created. Due to the inherit toughness and hardness of the material, this can be a time consuming and costly process.
China Ceramic Parts specialises in tight tolerance, highly complex work and has extensive in-house machining facilities – including 4th & 5th axis machining centres, drilling, grinding, milling, polishing, sawing, tapping, threading and turning – to enable us to manufacture Alumina components to the highest specifications.
China Ceramic Parts is your Alumina machining specialist for your technical ceramic prototyping & manufacturing needs; we are always happy to use our many years of advanced ceramics experience to provide advice on materials, design, and application. If you would like to buy Alumina plates, rods, tubes or custom machined components, please contact us and one of our experts will be happy to assist you.
Frequently Asked Questions
- What is Alumina used for?
Alumina is a very hard ceramic and is excellent at resisting abrasion. It is ideal for wear-resistant inserts or products. Alumina is commonly used as a high temperature electrical insulator, particularly the higher purity grades which offer better resistivity. Alumina also offers good resistance to strong acids and alkalis at elevated temperatures and is ideal for applications where resistance to corrosive substances is required. Some common applications of Alumina include:
- Wire and thread guides
- Mechanical seals (Seal faces, Valve seats)
- Machine components
- High temperature electrical insulators
- High voltage insulators
- Electronic components & substrates
- Ballistic armor
- Roller & ball bearings
- Wear resistant linings
- Semiconductor parts
- Laser cavities
- Tap plates
- Shot blast nozzles
- Knife sharpeners
- Precision shafts and axles in high wear environments
- What are the advantages of Alumina?
Alumina, also known as Aluminum Oxide, is a hard wearing advanced technical ceramic material frequently used in a wide variety of industrial applications. It features high hardness and wear resistance, low erosion levels, high temperature resistance, corrosion resistance, and bioinertness. Additionally, it can be highly polished making it useful for precision sealing applications like pumps and pistons. Alumina is an excellent high temperature ceramic material due to its high temperature stability. It is the most commonly used type of advanced ceramic and is available in purities ranging from 95 – 99.9%.
Some of the key advantages of Alumina include:
High Temperature Ability – Alumina can be used in both oxidizing and reducing atmospheres up to 1650°C (2900°F) and in vacuum environments up to 2000°C (3600°F).
Abrasion Resistant – Alumina is a very hard ceramic and is excellent at resisting abrasion. It is ideal for wear-resistant inserts or products.
Electrical Insulator – Alumina is commonly used as a high temperature electrical insulator, particularly the higher purity grades which offer better resistivity.
Chemical Resistance – Alumina offers good resistance to strong acids and alkalis at elevated temperatures and is ideal for applications where resistance to corrosive substances is required.
Additional properties and advantages of Alumina include
- High hardness
- Wear & abrasion resistant
- High compressive strength
- High mechanical Strength
- Resists strong acid and alkali attack at high temperatures
- Excellent electrical insulation properties
- Decent thermal conductivity